The Comprehensive Guide to Conveyor Covers
The Importance Of Conveyor Covers
Conveyor covers are not just an accessory — they’re a critical component of any material handling system. Here’s why:
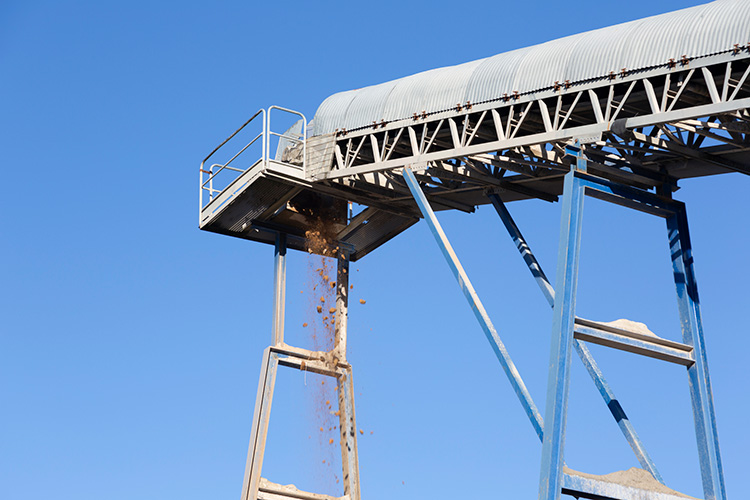
PROTECTING MATERIALS AND EQUIPMENT
Exposure to rain, snow, humidity, sun, and wind can seriously compromise conveyor systems and the materials they carry. Moisture can cause materials to freeze, clump, or degrade, while sun exposure weakens belts and rollers over time. Wind can blow lightweight product off the line, leading to loss and cleanup issues. Left unprotected, even the conveyor itself can rust or corrode.
Durable metal covers act as a shield, preserving product quality, preventing environmental damage, and extending the lifespan of critical conveyor components.
REDUCING MAINTENANCE AND DOWNTIME
When systems are left open to the elements, they wear out faster and require more frequent service. Conveyor covers help reduce rust, corrosion, and mechanical stress, which means fewer repairs, fewer belt replacements, and less unexpected downtime. That translates into greater operational efficiency and long-term cost savings.
IMPROVING WORKER SAFETY
Covered conveyor systems are safer conveyor systems. Covers reduce the amount of airborne dust released into the environment — a major health and visibility concern in many industrial settings. They also act as a physical barrier that helps prevent accidental contact with moving parts.
CONTAINING SPILLAGE AND CONTAMINATION
Covers also help maintain a clean, controlled work environment by containing dust, debris, and loose materials. This minimizes the risk of contamination, especially in applications where hygiene or environmental compliance is a concern.
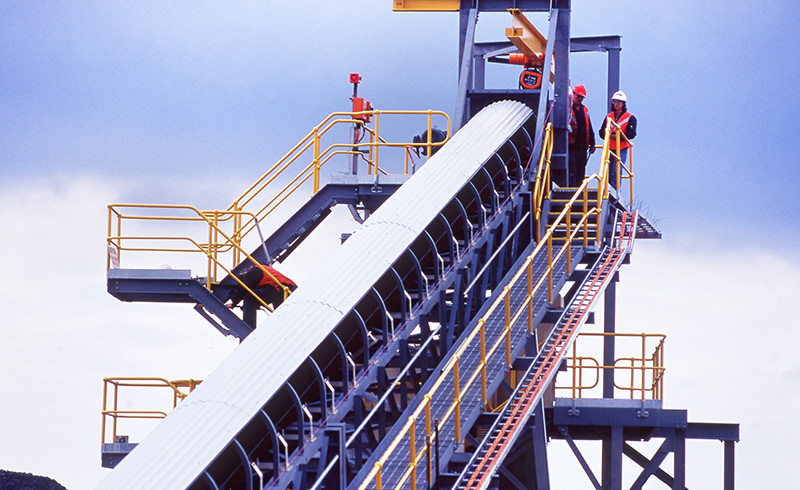
Why Corrugated Metal?
Custom vs. Standard Corrugated Metal Covers
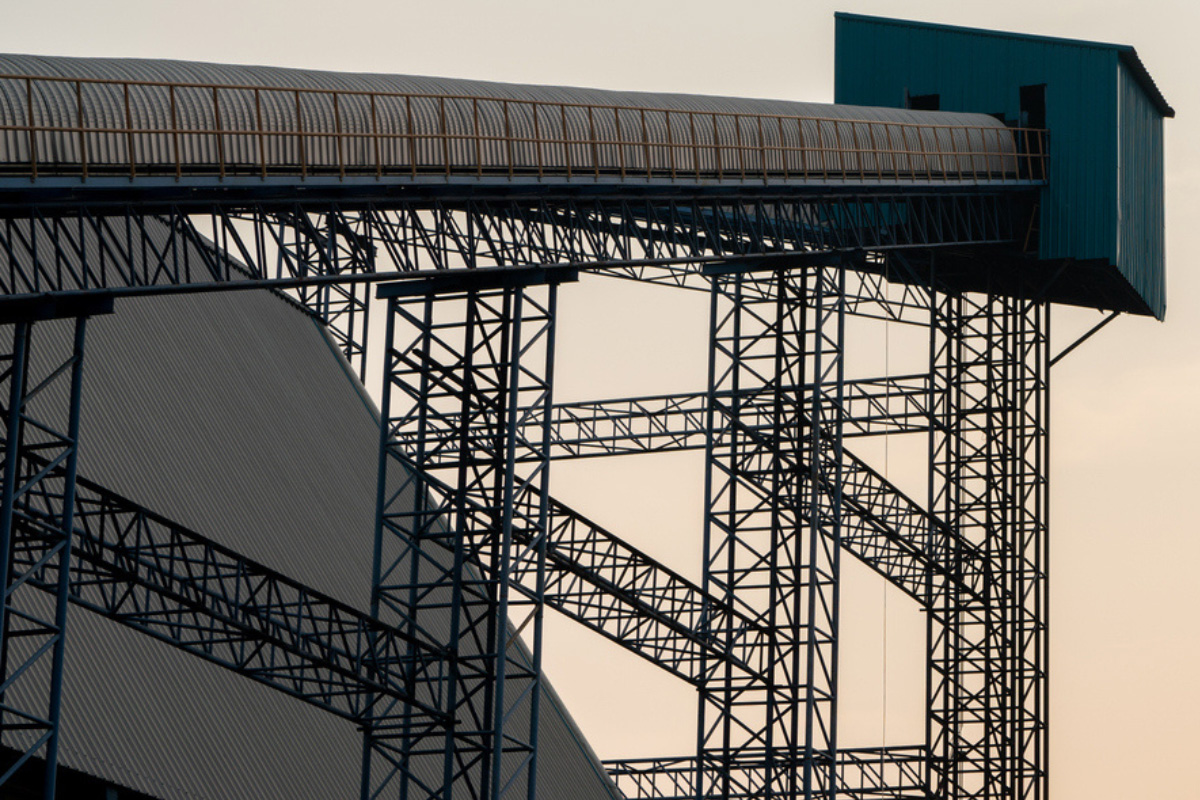
Custom Conveyor Covers
Custom covers are designed and fabricated to match your conveyor’s exact size, shape, and requirements. This is the best option if your system has unique widths, curves, or steep inclines. Custom covers are also ideal for challenging environments—such as facilities with frequent weather changes, high humidity, or strict hygiene standards.
With custom covers, you can add features like inspection hatches, hinged sections, or removable panels to make maintenance easier. You can also specify the material and finish for enhanced corrosion resistance or compliance with industry regulations. Custom covers are designed to fit your specific conveyor system. This is ideal for operations with:
- Unique widths, radii, or inclines
- Special environmental needs (e.g., marine, food processing)
- Requirements for inspection hatches, access doors, or special finishes
Custom covers ensure a precise fit and can solve challenges that standard options cannot. It’s worth considering custom covers if your conveyor has curves or changes in elevation, or if you need extra access points for maintenance. Additionally, they are well suited to corrosive or demanding environments.
Standard Conveyor Covers
Standard covers are pre-designed to fit common conveyor sizes and are often available for quick delivery. They’re a good choice if your operation uses typical conveyor layouts and doesn’t require special features.
Standard covers work best for:
- Your conveyors are straight, uniform, and use common dimensions
- You need a cost-effective, fast solution
- Your operation doesn’t require special access or features
The decision between custom and standard covers comes down to your conveyor layout, environment, and operational needs. If in doubt, consult with our team—we can help you evaluate your system and recommend the best solution.
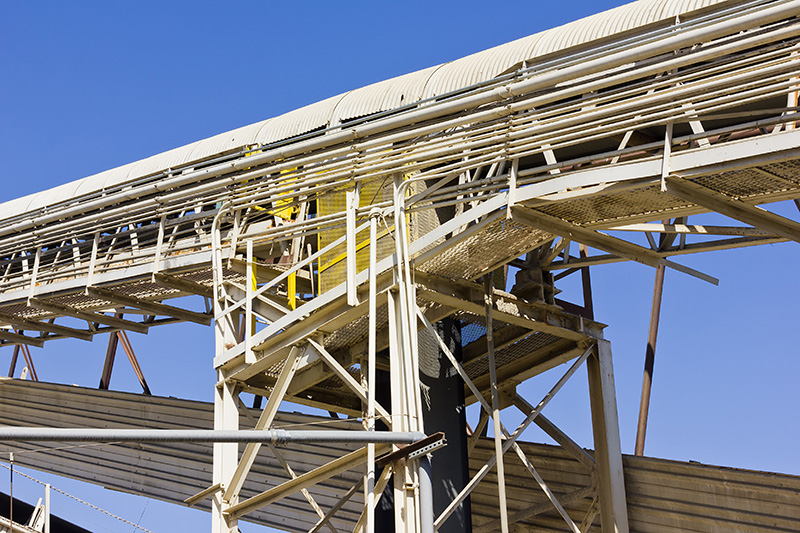
Material Choices: Galvanized Steel, Stainless Steel, or Aluminum?
The material you choose for your conveyor covers has a big impact on performance, durability, and long-term cost. At CMI, we offer three main options: galvanized steel, stainless steel, and aluminum. Here’s how to decide which is best for your operation:
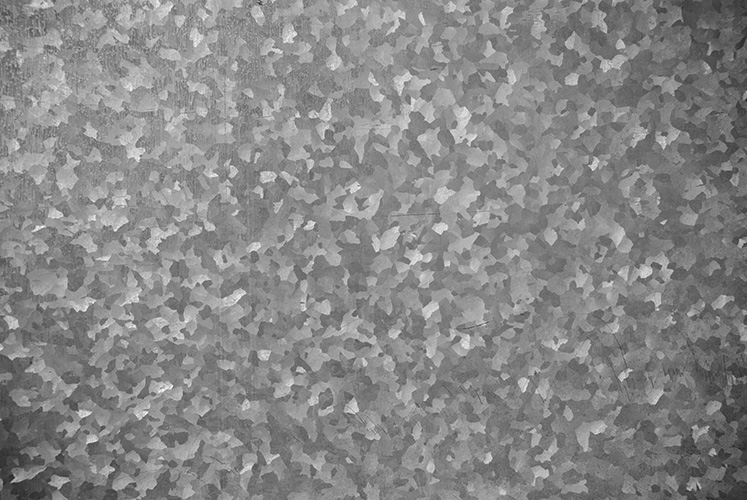
Galvanized Steel
Galvanized steel is the most popular choice for conveyor covers. It’s steel coated with a layer of zinc, which provides strong protection against rust and corrosion. This makes it ideal for outdoor conveyors or environments where moisture is present. Galvanized steel is strong, durable, and cost-effective. The corrugated profile increases rigidity, allowing covers to span longer distances without sagging or requiring extra supports.
Best for:
- Aggregate plants
- Mining operations
- General industrial sites
- Most outdoor applications
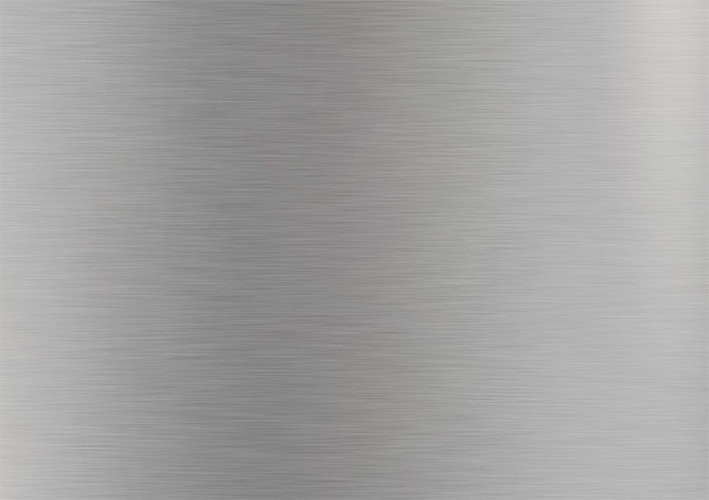
Stainless Steel
Stainless steel covers are chosen for their superior resistance to corrosion and chemicals. This material is especially important in industries where hygiene is critical, such as food processing, pharmaceuticals, and chemical manufacturing. Stainless steel stands up to frequent washdowns, exposure to harsh cleaning agents, and even saltwater environments. While it costs more than galvanized steel, the investment pays off in settings where product purity, regulatory compliance, or extreme durability are required.
Best for:
- Food processing
- Chemical manufacturing
- Marine environments
- Any application with strict hygiene or corrosion requirements
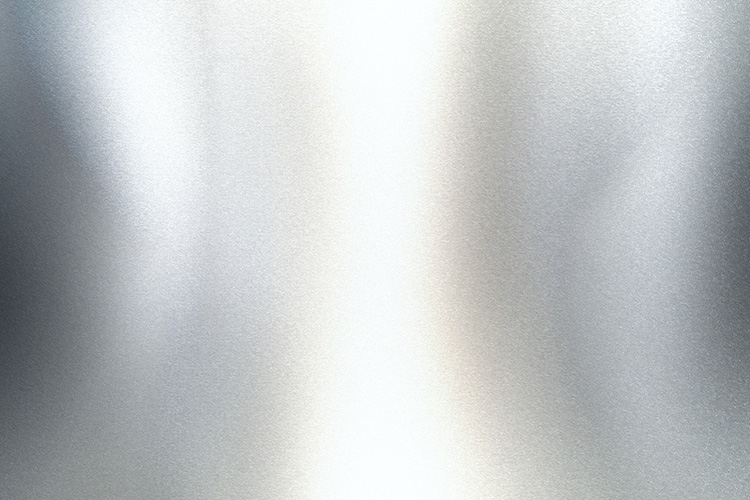
Aluminum
Aluminum covers are valued for their light weight and ease of handling. They are naturally resistant to corrosion, though not as robust as stainless steel in harsh chemical environments. Aluminum is often used for portable conveyor systems, light-duty applications, or situations where covers need to be removed and reinstalled frequently. Its lower weight can also reduce the load on conveyor supports and make installation faster and easier.
Best for:
- Portable conveyor systems
- Temporary installations
- Light-duty conveyors
- Applications where quick removal is needed
No matter which material you choose, CMI forms each into a corrugated profile. This not only increases the material’s strength and rigidity but also allows for longer spans between supports and better resistance to impact or deformation.
Key Design Factors for Conveyor Cover Systems
A well-designed conveyor cover system is about more than just picking the right material. Several factors influence performance, accessibility, and longevity.
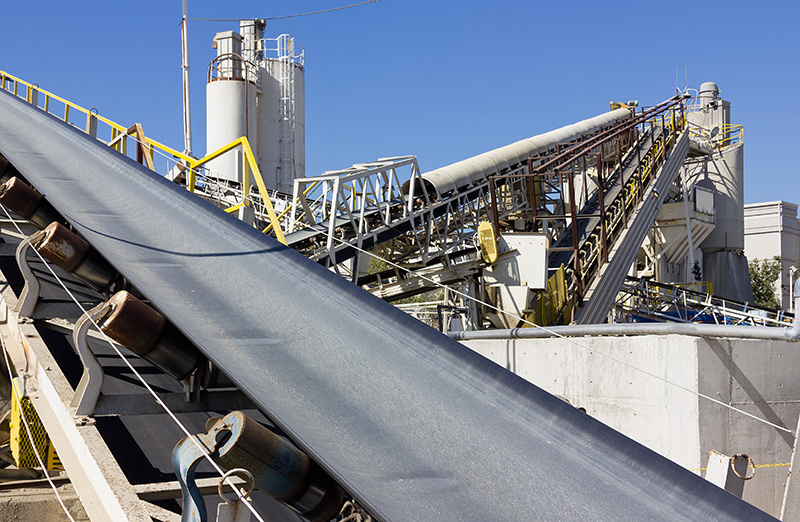
Conveyor Layout and Incline
If your conveyor has curves, changes in elevation, or steep inclines, you may need custom covers. Steep conveyors might also need special belting and cover shapes to prevent material rollback and keep the system running smoothly.
Environmental Conditions
Outdoor conveyors need materials that can handle rain, snow, and sun. In corrosive or chemical environments, stainless steel or coated metals are best. For very hot or cold settings, consider insulation or special finishes to protect both the conveyor and the materials being transported.
Access and Maintenance
Inspection hatches, hinged sections, and removable panels make it easier to inspect, clean, and maintain your conveyor. Planning for access can save time and reduce downtime. Well-designed covers should allow for safe, quick access without compromising protection.
Span and Support
Corrugated metal’s strength allows for longer spans between supports, which can simplify installation and reduce costs. However, very wide conveyors may still need extra bracing or engineered supports to maintain rigidity and stability.
Safety and Compliance
Covers should help prevent accidental contact with moving parts and control dust and noise, supporting a safer workplace and regulatory compliance. In industries with strict standards, such as food or pharmaceuticals, covers must also be easy to clean and resistant to contamination.
The Importance of High-Quality Conveyor Supports
A well-designed conveyor cover system is about more than just picking the right material. Several factors influence performance, accessibility, and longevity.
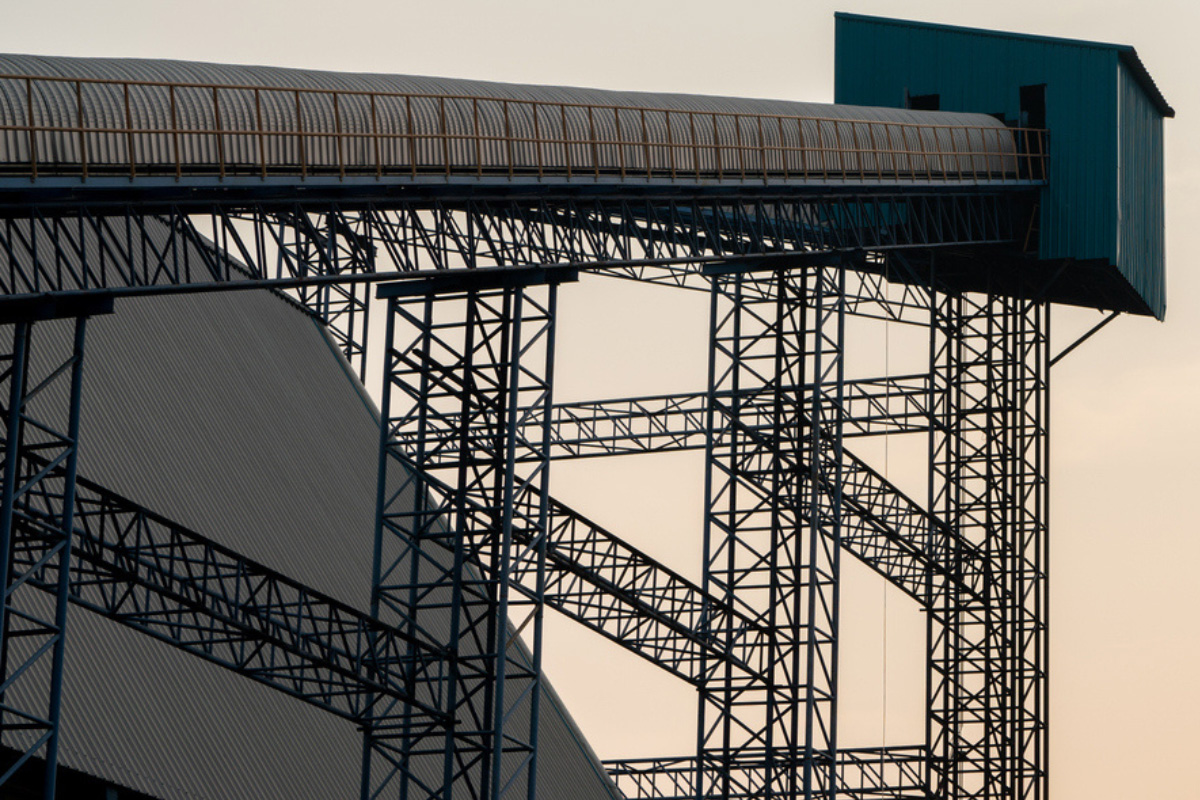
Conveyor supports are just as important as the covers themselves. They provide the stable, level foundation your conveyor needs to run efficiently. High-quality supports reduce noise and vibration, help keep belts aligned, and protect against heavy loads or impacts. Modular supports and impact beds make maintenance easier and can extend the life of both the belt and the covers.
Investing in durable, well-designed supports helps prevent downtime and reduces maintenance costs. Good supports also improve safety by keeping the conveyor stable and minimizing the risk of breakdowns. For any operation that relies on material handling systems, reliable supports are a smart investment.
Practical Examples
How Conveyor Covers Solve Real-World Problems
A well-designed conveyor cover system is about more than just picking the right material. Several factors influence performance, accessibility, and longevity.
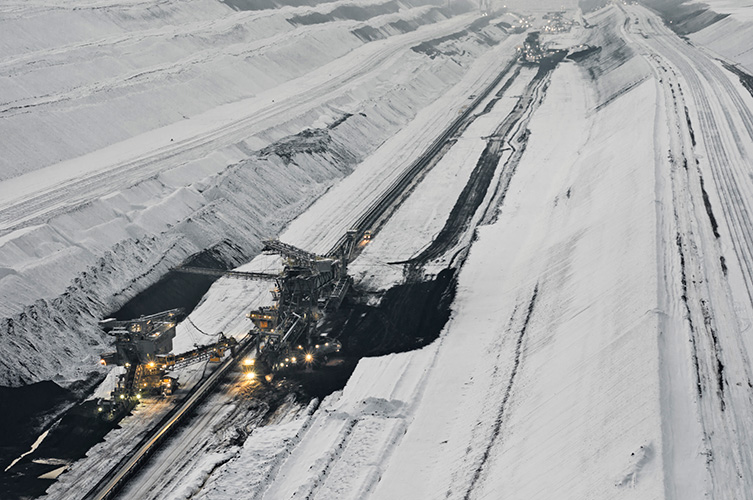
Example 1: Aggregate Plant in a Harsh Climate
A Midwest aggregate facility needed to protect its conveyor from rain and snow, which caused material to freeze and stick to the belt. CMI supplied galvanized corrugated covers with custom inspection hatches, reducing downtime and improving throughput.
Example 2: Food Processing Facility
A food manufacturer required stainless steel covers to meet hygiene standards and withstand frequent washdowns. Custom covers with quick-release fasteners made cleaning and inspection fast and easy.
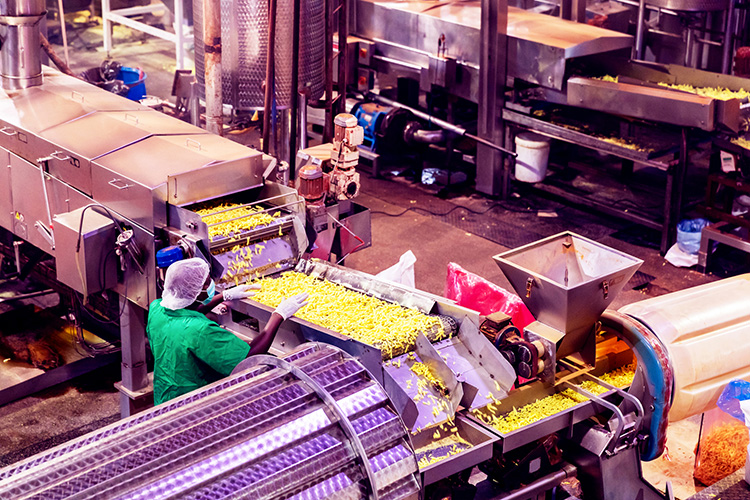
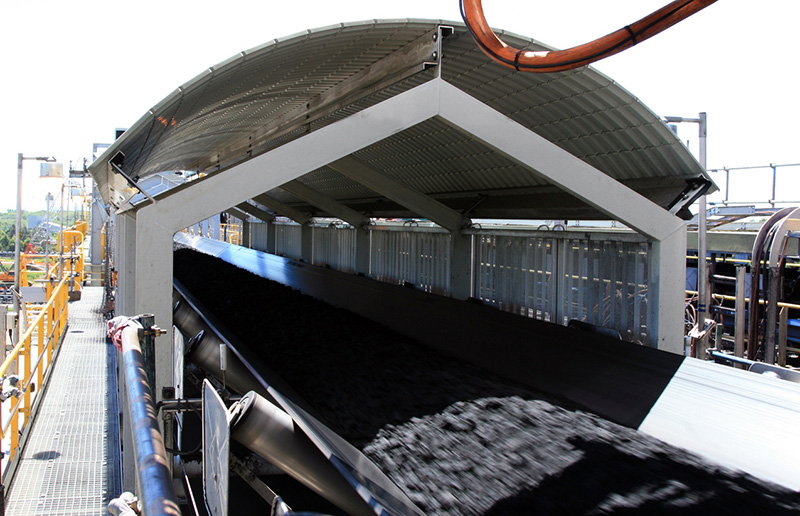
Example 3: Portable Conveyor System
A contractor needed lightweight, removable covers for a portable conveyor used on multiple job sites. Aluminum corrugated covers provided the right balance of protection and mobility.